Well, I guess I've always had sort of a tool fetish. Bonafide tool-a-holic, I suppose.
A while back I added another tool cabinet and decided to rearrange everything to try to make the tools more organized and accessible. Of course, now I can't find any of them without opening at least half of the drawers, but that's another story.
Anyway, I saw these pretty neat looking socket organizers at the local Sears store a while back, and decided to get a complete set of them for both metric and SAE sockets. Both 6 point and 12 point versions. 1/2 inch, 3/8 inch, and 1/4 inch. Standard and deep sockets. Suddenly that LOT of sockets I thought I had didn't seem like such a LOT any longer.
The bunch of sockets I had were just laying around in drawers, so I really didn't have any good idea of which ones I might or might not have. So I figured organizing them would have me a great idea. Losing a socket would be a thing of the past, because each would have a place where it HAD to go when I put them in the tool cabinets.
But I didn't realize how overpowering it would be to see the HOLES in my "collection" of sockets that I DIDN'T have and have this compelling urge to fill them. Kind of felt like an itch some place I couldn't scratch every time I would open up one of the socket drawers. I resisted for a while, thinking it was just silly, but the itch just got worse over time. My eyes were always instantly drawn to the empty pegs pointing accusingly at me that they were neglected by being empty. So is this some sort of tool OCD affliction?
OK, so I surrendered and figured I would just complete one tray at a time by ordering what I needed and fix this problem gradually. Sockets are really quite expensive when you get right down to it and *need* a bunch of them. I never would have thought I was so socket deficient. Actually I can never remember NOT coming up with a socket I needed when I needed it, so this is really pretty baffling.
Advance Auto always seems to have some sale going on with free shipping, and they tend to sell pretty good brand name tools from what I've seen. So a couple of weeks ago ordered about a dozen individual sockets from them. I completed the order online after finding the ones I needed for the first tray, and not long afterwards started getting notices of them being shipped. One at a time. One notice for each socket I ordered. I figured it must be just the way their ordering system works, and I would get a box with them all inside. But nope. UPS delivered a dozen boxes all with a single socket inside. :shrugs:
Pretty ridiculous way to do it, as I'm sure they had to lose money that way, but whatever. I figured maybe it was just a fluke.
I do have to admit that it was strangely satisfying to me when I put those new sockets on those empty pegs. And yes, I did polish them to make them shine.
So the other day I got a $50 discount coupon sent to me, and I figured I could order another batch of sockets, as the itch was building up again. Ordered 14 of them this time. Would have gotten more, but they were out of stock on some I wanted, er NEEDED. With the coupon I'm getting them at half price plus getting free shipping, so it actually is a pretty good deal.
So lo and behold UPS delivered a box today from Advance Auto, and yep, you guessed it. It had ONE socket inside. :crazy01: So I guess I've got 13 more boxes that will be showing up over the next several days. The UPS driver is probably not going to be thinking very kindly about me. I WILL not tell him what is inside of them all.
Anyway I can't see how Advance Auto can possibly be making any money like this, but heck, if you ever want to give someone a LOT of Christmas presents some year, order them a set of sockets in this manner from Advance Auto. I'm sure it will look impressive under the Christmas tree, and they will have LOTS of presents to open up Christmas morning.
In any event, I almost have the metric sockets complete, so I'll be working on the SAE sockets the next time AA has a good sale. Too bad I don't have anything worthwhile to do with all those little boxes I'm getting, though. I do hate just throwing them into the recycling bin from WastePro.
A while back I added another tool cabinet and decided to rearrange everything to try to make the tools more organized and accessible. Of course, now I can't find any of them without opening at least half of the drawers, but that's another story.
Anyway, I saw these pretty neat looking socket organizers at the local Sears store a while back, and decided to get a complete set of them for both metric and SAE sockets. Both 6 point and 12 point versions. 1/2 inch, 3/8 inch, and 1/4 inch. Standard and deep sockets. Suddenly that LOT of sockets I thought I had didn't seem like such a LOT any longer.
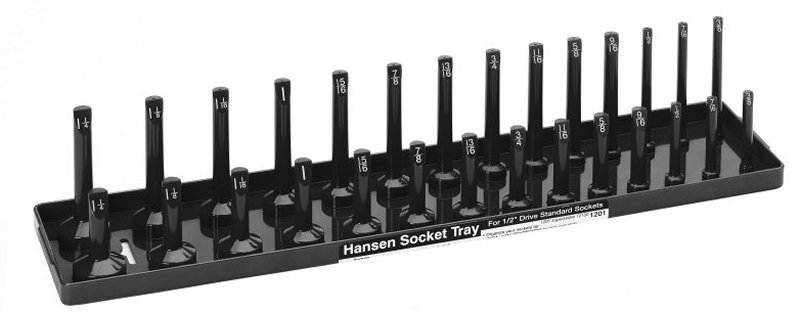
The bunch of sockets I had were just laying around in drawers, so I really didn't have any good idea of which ones I might or might not have. So I figured organizing them would have me a great idea. Losing a socket would be a thing of the past, because each would have a place where it HAD to go when I put them in the tool cabinets.
But I didn't realize how overpowering it would be to see the HOLES in my "collection" of sockets that I DIDN'T have and have this compelling urge to fill them. Kind of felt like an itch some place I couldn't scratch every time I would open up one of the socket drawers. I resisted for a while, thinking it was just silly, but the itch just got worse over time. My eyes were always instantly drawn to the empty pegs pointing accusingly at me that they were neglected by being empty. So is this some sort of tool OCD affliction?
OK, so I surrendered and figured I would just complete one tray at a time by ordering what I needed and fix this problem gradually. Sockets are really quite expensive when you get right down to it and *need* a bunch of them. I never would have thought I was so socket deficient. Actually I can never remember NOT coming up with a socket I needed when I needed it, so this is really pretty baffling.
Advance Auto always seems to have some sale going on with free shipping, and they tend to sell pretty good brand name tools from what I've seen. So a couple of weeks ago ordered about a dozen individual sockets from them. I completed the order online after finding the ones I needed for the first tray, and not long afterwards started getting notices of them being shipped. One at a time. One notice for each socket I ordered. I figured it must be just the way their ordering system works, and I would get a box with them all inside. But nope. UPS delivered a dozen boxes all with a single socket inside. :shrugs:
Pretty ridiculous way to do it, as I'm sure they had to lose money that way, but whatever. I figured maybe it was just a fluke.
I do have to admit that it was strangely satisfying to me when I put those new sockets on those empty pegs. And yes, I did polish them to make them shine.
So the other day I got a $50 discount coupon sent to me, and I figured I could order another batch of sockets, as the itch was building up again. Ordered 14 of them this time. Would have gotten more, but they were out of stock on some I wanted, er NEEDED. With the coupon I'm getting them at half price plus getting free shipping, so it actually is a pretty good deal.
So lo and behold UPS delivered a box today from Advance Auto, and yep, you guessed it. It had ONE socket inside. :crazy01: So I guess I've got 13 more boxes that will be showing up over the next several days. The UPS driver is probably not going to be thinking very kindly about me. I WILL not tell him what is inside of them all.
Anyway I can't see how Advance Auto can possibly be making any money like this, but heck, if you ever want to give someone a LOT of Christmas presents some year, order them a set of sockets in this manner from Advance Auto. I'm sure it will look impressive under the Christmas tree, and they will have LOTS of presents to open up Christmas morning.
In any event, I almost have the metric sockets complete, so I'll be working on the SAE sockets the next time AA has a good sale. Too bad I don't have anything worthwhile to do with all those little boxes I'm getting, though. I do hate just throwing them into the recycling bin from WastePro.